What Is PCB Router Depaneling
PCB router depaneling is a precise and efficient method for separating individual circuit boards from a larger panel using a high-speed routing bit. It ensures minimal mechanical stress, smooth edges, and the ability to handle intricate designs, making it ideal for high-quality electronics manufacturing.
Advantages of PCB Router Depaneling
Precision & Quality
PCB router depaneling provides clean, smooth cuts with minimal rough edges, ensuring high-quality results. This is important for maintaining the performance of sensitive components, especially in high-density designs where precise cutting is necessary.
Component Safety
The router method applies minimal mechanical stress, which helps protect delicate electronic components like surface-mount devices (SMDs) from damage. This ensures that sensitive parts remain intact during the depaneling process.
Shape Flexibility
PCB router cutting can handle complex, curved, or irregular shapes, making it suitable for a variety of designs. This is especially helpful in industries like automotive and medical devices, where custom-shaped PCBs are often needed.
Clean & Low-Dust Process
Unlike some other cutting methods, PCB router depaneling creates less dust and debris. The built-in vacuum systems help keep the workspace clean, which is important for maintaining quality and safety, especially in controlled environments.
Efficient for Mass Production
PCB router depaneling is great for high-volume production because it can be automated. This allows for continuous operation, faster production, and less manual work, making it ideal for manufacturing large quantities of PCBs quickly and consistently.
No Heat Damage
Unlike laser cutting, which can generate heat and potentially damage components, PCB router depaneling doesn’t produce excessive heat. This helps protect sensitive components and the PCB material itself from heat-related issues.
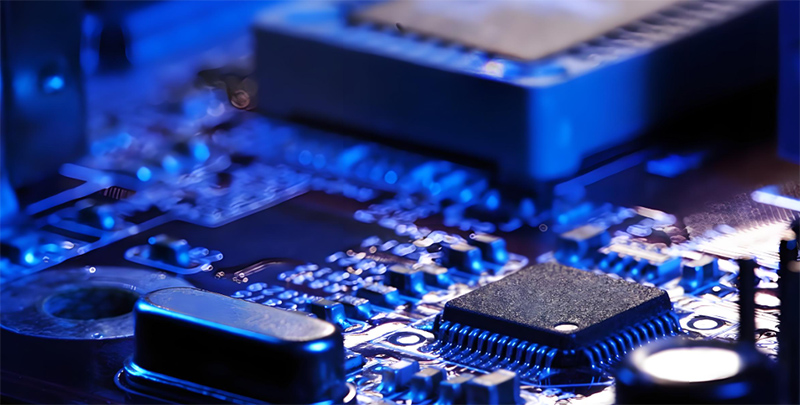
Cost-Effective
While the initial cost of the equipment may be higher, PCB router depaneling reduces labor costs and improves efficiency, making it a cost-effective solution for both small and large production runs. It also eliminates the need for custom tooling, saving money in the long run.
Suitable for High-Density PCBs
This method works well for high-density PCBs with components located close to the edges. It ensures that the components are not damaged during the depaneling process, which can be a problem with other methods like punching or V-scoring.
Disadvantages of PCB Router Depaneling
Higher Equipment Cost
Requires investment in specialized CNC routing machines.
Slower Than Laser Depaneling
Mechanical routing takes longer compared to laser cutting, especially for intricate designs.
Tool Wear and Maintenance
Router bits wear out over time and need regular replacement to maintain precision.
Dust and Debris Generation
Cutting produces dust, which requires proper vacuum systems for cleanliness and safety.
Limited to Certain Materials
Less effective for very thin or highly flexible PCBs compared to laser depaneling.
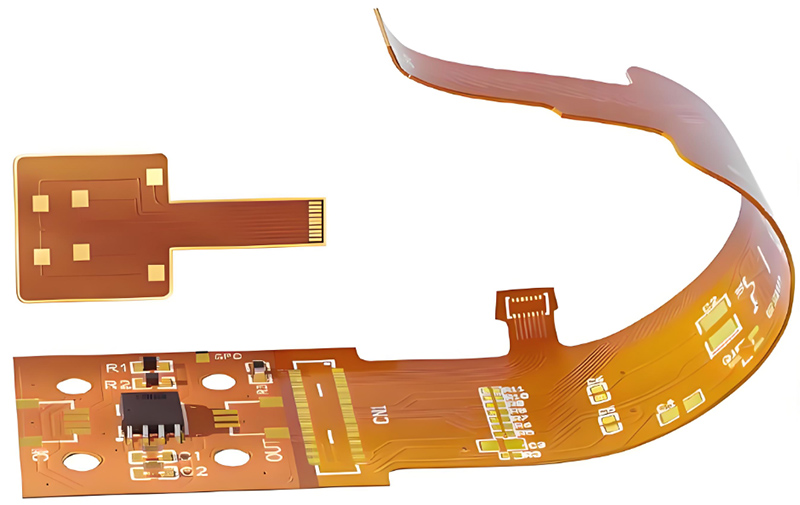
Potential Thermal Impact
Friction from high-speed routing can generate heat, which may require careful process control.
How to Select Router Cutting for PCB Depaneling
Precision & Cutting Quality
Look for high-speed spindles (30,000–60,000 RPM) for smooth, burr-free edges. Choose machines with vision alignment systems for accurate cutting.
Board & Panel Compatibility
Ensure the machine supports your PCB size, thickness, and material (FR4, aluminum, flex, etc.).Check for adjustable fixture systems to handle various board layouts.
Automation & Throughput
For high-volume production, opt for fully automated systems with robotic loading/unloading. Semi-automatic models are ideal for small to medium batches.
Dust Management
A built-in vacuum system is essential to reduce debris and maintain clean cuts.
Software & Programming
Look for user-friendly CAD/CAM software for easy programming of cutting paths.
Maintenance & Cost Efficiency
Consider tool wear rates and ease of spindle/bit replacement. Balance initial cost vs. long-term durability based on production needs.
Advantages of Seprays’PCB Router Machine
●Clamping fixtures are used for holding during cutting, with no separate jigs for board separation.
●Bottom-side cutting design, suitable for PCBs with tall top-side components, supporting heights up to 45mm.
●CCD vision alignment with compensation correction ensures high cutting precision.
●The output can place boards in a 0-180-degree array.
●Supports multiple PCB handling options, including conveyor belt, track system, and custom tray output.
Seprays’ PCB Router Depaneling Solutions
GAM 380AT Gripper In-Line Automatic PCB Bottom Depaneling Machine
The GAM 380AT Gripper In-Line Automatic PCB Bottom Depaneling Machine by SEPRAYS is a high-precision and versatile solution designed for efficient and precise depaneling of printed circuit boards (PCBs).
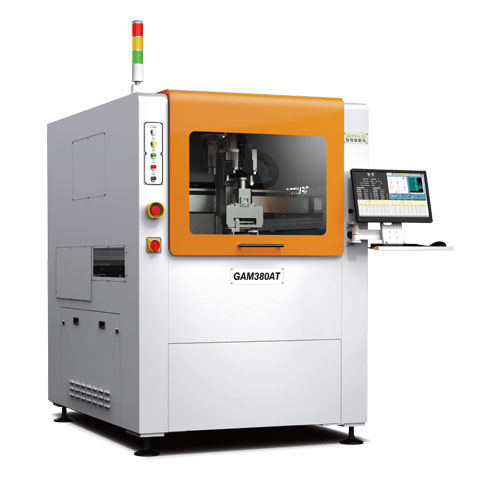
Conclusion
When selecting a PCB router depaneling system, it’s essential to consider factors like cutting precision, automation, dust control, and long-term costs. While router depaneling can require a higher upfront investment and ongoing maintenance, it offers high-quality and reliable separation of PCBs. Advanced machines, such as Seprays’ PCB routers, provide features like vision alignment and automated handling, ensuring accurate results. By understanding both the advantages and challenges, manufacturers can find the right solution to meet their production needs.